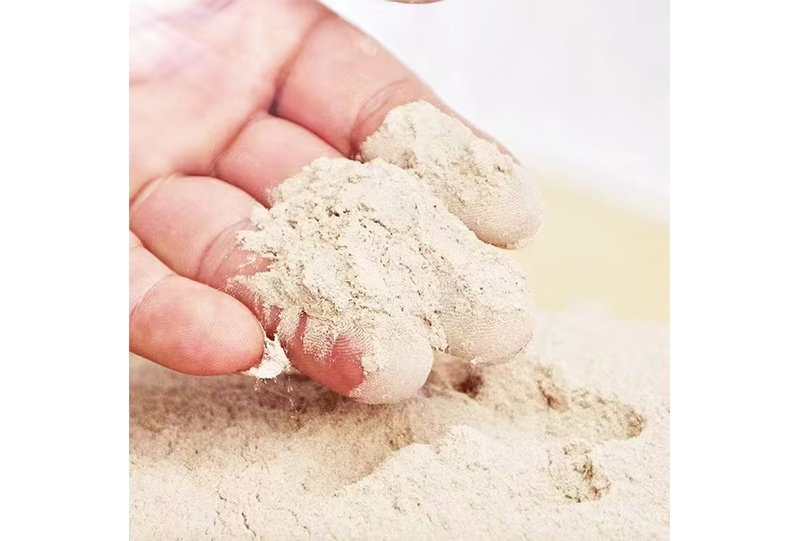
Coating for Lost Foam Casting Process
Castchem’s coating material are made of Aluminosilicate and Andalusite as the main chemical components, which are refractory coatings with high air permeability. It is mainly used for STMMA and EPS foam mould coatings for steel lost foam castings.
The high viscosity of the coating provides special anti-flux performance, resulting in a smooth, strong coating with no dripping, cracking or wrinkling in the appearance of the impregnated coating. The coating is also available in a wide range of water dilutions, allowing the optimum coating thickness to be found for various casting requirements.
The thickness of the product can be up to 20000mpa.s, but the viscosity is reduced immediately after complete drying, which means it can be easy to be stripped from mold. Meanwhile, it can eliminate the metal penetration and rich carbon and other defects in castings and reduce the surfaces cleaning workings
Get the latest price Get a free Sample
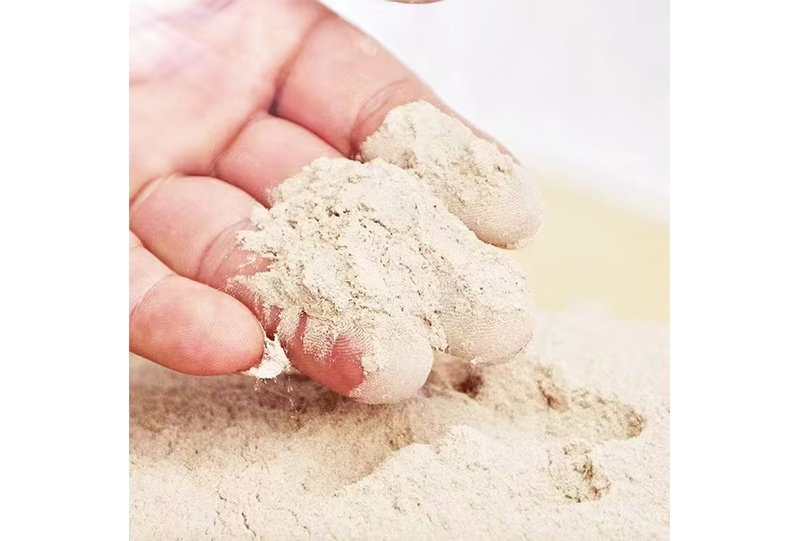


1. Characteristic:
CASTCHEM’s LFC refractory coatings are highly permeable refractory materials for ductile iron and steel castings.The coatings have a high viscosity with exceptional anti-flow properties, resulting in a smoother, stronger coating that will not crack or wrinkle after coating. The coating has a very wide range of water dilutions to find the optimum coating thickness for manufacturers to eliminate metal penetration and carbon-rich defects to eliminate surface cleaning issues.
2. Physical properties of finished products:
Appearance: Powder
Color: Grey brown
Refractory material: Aluminosilicate
Solvent: Water
Net wet/Bag: 25kgs.
Refractoriness: 1700℃
Air permeability: 0.6mm-260, 0.8mm-210,1.0mm-140
3. Directions:
1. High-speed Mixing: Coatings : Water= 1:0.65 to 0.68. Add water into the bucket until until the fan is immersed, adjust the stirring speed to 400 r/min and add coatings slowly. After adding all coatings, adjust to 600 r/min and keep mixing for 2 hours. Pay attention to the state of the coatings slurry, the coating slurry’s Baume degree should between 65 to 73 degrees, and then stir continuously at 400 r/min for 1 hour.
Operators should keep daily records, from which to find the optimal dosage of water and coatings.
2. Low-speed Mixing: Slow pre-mixing for 10 minutes (especially for new unused tubs). High-speed mixing for thick coating must be diluted with water. The agitator is equipped with a variable-speed motor, a container with considerable capacity , and a ring plate device. The stirring speed is 10-60 revolutions per minute. The ideal agitation speed depends on the type of coating and the size of the tank. After finding the desired speed, the stirring should be carried out at the desired speed. The coating shall be modulated to a concentration of between 65 and 73 Baume degrees. The Baume degrees of the coating shall be varied depending on the wall thickness, dimensions and complexity of the casting. The Baume degrees also varies with temperature. Baum degrees is slightly lower due to lower temperatures in winter, for the same reason, Baum degrees is higher in summer. We recommend that factories should find the optimum result in terms of pack degree and percentage of coating content according to actual conditions, and try to control these conditions to maintain the quality of the castings. It should be noted that the viscosity will be affected by the temperature and the stirring speed, the viscosity will affect the value of the Baume degrees, reduce the value of Baume degrees will reduce the attached solid coatings on the foam-pattern.
3. Coating: CASTCHEM's iron coating materials for foundry chemistry are very sensitive to shear strength, i.e., their viscosity varies with mixing speed. Therefore, the weight of the slurry deposited on the surface of the foam pattern during immersion is affected by the stirring force. In order to obtain high quality castings, the stirring speed and Baume degree should be well controlled. We recommend using dipping water as a mixing agent. Some plants can be mixed continuously for a period of time and then dipped. The viscosity will increase rapidly for a period of time just after the mixing has stopped and then gradually stabilize. Additionally, the immersion rate, dwell time and removal rate of the pattern are also very important. For complex castings, the mould should be ensured that air bubbles do not remain during the dipping process.
4. The Main Specification of Castchem’s Coatings Material
Appearance |
Faint yellow powder |
Refractory material |
Aluminosilicate and Andalusite |
Mesh size |
60~80 |
Density |
≤1.10g/cm³ |
Solvent |
Water |
Net weight(Packing) |
25 kg/bag |
Moisture content |
≤1.0% |
Viscosity(6 roll/min) |
≥20Pa.s |
Radioactivity |
According to GB6566 |
If you require any additional materials or information, I will be more than happy to supply it.
Hope to be your best partner.
Tel:+86 17857651655
Whats app/ WeChat: +86 17857651655
Email:eowyn@zj-castchem.com
International Sales Department: Eowyn Jiang